How Much Does a WMS Cost?
A Complete Breakdown of Warehouse Management System Expenses.
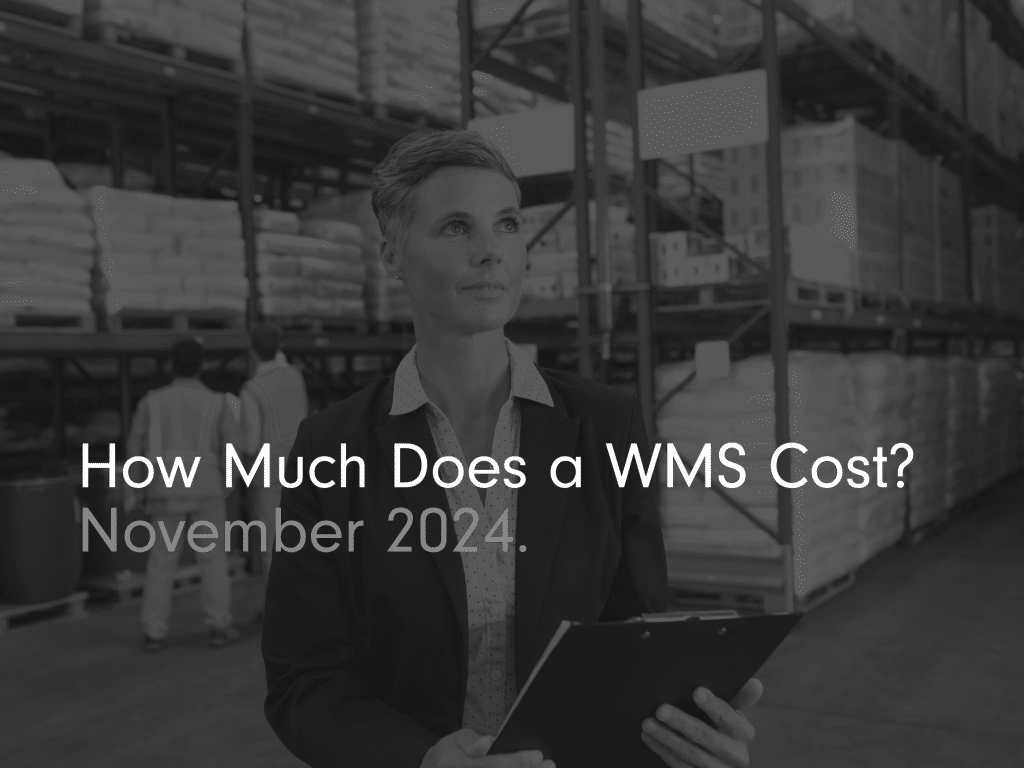
When businesses consider implementing a Warehouse Management System (WMS), one of the most pressing questions is, “How much does a WMS system cost?” The answer is multifaceted and involves understanding various factors, including software licensing, hardware needs, implementation, training, and ongoing support costs.
In this article, we will look at the parts of WMS pricing. We will discuss the total cost of ownership. We will also share how these costs can change based on your needs. Factors include the number of users, the type of system (cloud-based or on-premise), and extra features.
1. Understanding WMS Software Costs: Cloud-Based vs. On-Premise Solutions.
The WMS cost largely hinges on the type of licensing model chosen. Businesses typically have two options: cloud-based WMS and on-premise solutions. Each has its own pricing structure that impacts the upfront costs and long-term financial commitments.
- Cloud-Based WMS: This model operates on a subscription basis, meaning companies pay a recurring fee. Subscription costs usually range from £1,000 to £10,000 per month, depending on factors such as the number of users and the complexity of features. For example, a cloud-based WMS may charge a license fee that scales with the number of users. Typically, the pricing model allows for flexibility, making it easier for businesses to adjust their subscription based on their operational needs.
- On-Premise Solutions: On-premise WMS generally involves a perpetual license, which requires an upfront cost that can vary significantly depending on the system’s capabilities and customisation. While this may seem high, the ongoing support costs are usually lower compared to cloud-based options, as the business retains control over the software and its updates. However, the responsibility for hardware, installation, and ongoing maintenance falls solely on the company.
Understanding the differences in WMS pricing is crucial for businesses to choose the best fit for their operational model.
2. WMS Tiers: Understanding Different Levels of Functionality.
WMS solutions are typically categorised into tiers based on functionality and complexity, each corresponding to different pricing models. Understanding these tiers can help businesses identify the right system for their specific needs and budget.
- Tier 1 (Enterprise WMS): Tier 1 WMS solutions are made for large organisations with complex operations. They provide strong features like advanced inventory management, order management, and customisable workflows. These systems can handle multiple warehouses and large inventories. They also integrate with other enterprise systems. The average cost for Tier 1 solutions ranges from £100,000 to over £500,000 for licensing and setup. These systems usually require a long-term commitment because they are complex and need customisation. Companies using these systems often have many users and high order volumes. This makes a sophisticated WMS necessary to meet their logistical needs.
- Tier 2 (Mid-Market WMS): Mid-market solutions are suitable for growing businesses that need more advanced features than basic systems but do not require the full complexity of Tier 1 solutions. These WMS can typically handle up to 20-50 users and are priced between £20,000 and £100,000, depending on the number of users and additional functionalities. Companies in this tier may have moderate order volumes and complexity in their operations, making these systems an ideal fit for businesses in transition or growth.
- Tier 3 (Entry-Level WMS): Targeting smaller businesses or those with simpler operations, Tier 3 WMS solutions provide basic functionalities for effective warehouse operations. These systems typically offer essential features like order tracking, inventory control, and basic reporting. The cost for these solutions can range from £5,000 to £20,000, making them more accessible for smaller organisations. Typically, these businesses operate with fewer users and lower order volumes, allowing them to utilise simpler systems without sacrificing operational efficiency.
Choosing the right tier of WMS is crucial and often depends on company size, the number of users, and order volume. Businesses should assess their current operations and future growth potential to ensure they invest in a solution that supports their evolving needs.
3. Implementation Costs: Setting Up for Success.
Implementation costs play a vital role in determining the overall WMS software costs. These expenses can range from £20,000 to upwards of £100,000, depending on various factors, such as system complexity, data migration requirements, and the need for custom features.
- Data Migration: Moving existing data into the new system is essential for a seamless transition. This process can account for 10-20% of the total implementation costs, depending on the amount and quality of the data involved.
- Customisation: Tailoring the WMS to fit specific workflows or operational requirements can lead to additional costs. For instance, if your business manages multiple warehouses, integrating these operations into the WMS might necessitate custom coding and setup, potentially increasing the license costs by £5,000 to £20,000.
- Training: Another important cost is preparing your team to use the new system effectively. Training can range from £1,000 to £10,000, depending on the number of users and the complexity of the software. Proper training ensures that your team can leverage all the features for efficient inventory and order management.
By investing in a thorough implementation process, businesses can significantly enhance the effectiveness of their WMS, resulting in smoother warehouse operations.
4. Hardware and Additional Costs: The Tools That Support Your WMS.
Implementing a WMS often requires complementary hardware investments. The costs associated with hardware will vary based on the size and scope of the warehouse operations.
- Barcode Scanners and Mobile Devices: These are essential tools for effective inventory tracking and order processing. Costs can range from £300 to £2,000 per scanner, while mobile devices typically range from £500 to £1,500.
- Label Printers and RFID Technology: Many businesses need label printers to manage inventory efficiently. These printers usually cost between £300 and £1,200, while RFID systems for real-time tracking can range from £10,000 to £50,000 depending on the extent of the implementation.
- Servers for On-Premise Solutions: If using an on-premise WMS, businesses will need dedicated servers, which can add another £5,000 to £20,000 to the overall cost.
In total, additional costs for hardware can range from £5,000 to £50,000 or more, depending on your warehouse’s technology needs and operational scale.
5. Ongoing Maintenance and Support Costs: Keeping Your WMS Running Smoothly.
- Cloud-Based WMS: With this model, ongoing maintenance, updates, and technical support are typically included in the subscription costs. This means that businesses can expect predictable monthly or annual costs without unexpected financial burdens.
- On-Premise WMS: In contrast, businesses that opt for on-premise solutions will incur ongoing support costs. This typically amounts to 15-20% of the initial licensing fee annually. This fee covers critical system updates, security patches, and technical support, ensuring that the WMS remains secure and functional.
By planning for ongoing support costs, businesses can budget effectively and maintain system performance over time.
6. Calculating ROI: Assessing the Value of Your WMS Investment.
Understanding the cost of a WMS is important. However, the real value of a WMS is in improving inventory and order management. Companies that use a WMS can achieve a strong return on investment. This comes from better efficiency and fewer errors.
For example, businesses that adopt a WMS often report:
- Inventory Accuracy: Improvements in inventory accuracy can reach up to 99%, reducing costly errors associated with stockouts or overstocking.
- Order Picking Efficiency: Many companies see an increase in order picking efficiency of 25% or more, resulting in significant labour savings. Depending on the size of the operation, this can translate to savings of nearly £50,000 per year.
- Customer Satisfaction: Enhanced order accuracy and faster fulfilment times lead to higher customer satisfaction, resulting in repeat business and positive referrals. Companies often find that reducing order inaccuracies leads to fewer returns, saving on costs related to handling and processing returns.
By considering these factors, businesses can evaluate the long-term benefits of a WMS investment, which often leads to a positive ROI within the first few years of implementation.
7. Hidden Costs: What to Watch For.
As businesses consider the total cost of implementing a WMS, it’s essential to account for potential hidden costs that may arise:
- Future Upgrades: Many WMS vendors offer additional modules that provide enhanced functionality, which can be necessary for future growth. These upgrades may come with additional costs that need to be factored into the budget.
- Custom Integrations: Integrating a WMS with existing systems like ERP or TMS often involves custom development work, which can add significant costs depending on the complexity of the integrations.
- Operational Changes: As businesses evolve, operational changes may require adjustments to the WMS. Planning for future scalability and flexibility in your WMS can help mitigate unexpected expenses.
Balloon One’s Tier 1 and Tier 2 WMS Solutions: A Flexible Fit for Your Business Needs
At Balloon One, we offer Körber WMS solutions that seamlessly fit into both Tier 1 and Tier 2 categories. These robust systems provide businesses with scalable, flexible options that meet the unique requirements of different operational levels.
For Tier 1 enterprises, our Körber WMS solution delivers advanced features necessary to support complex, high-volume operations. With strong integration capabilities, customisable workflows, and multi-site management, our Tier 1 WMS is designed for large organisations that require sophisticated logistics support. This solution helps businesses optimise their supply chain, improve inventory accuracy, and streamline order fulfilment.
For growing businesses, our Tier 2 WMS offering delivers powerful features at a more accessible cost. Ideal for mid-market companies that are scaling their operations, this solution ensures smooth warehouse management without the complexity or price tag of a Tier 1 system. With intuitive interfaces and advanced functionality, our Tier 2 WMS is perfect for businesses looking to improve efficiency as they expand.
Conclusion: Making an Informed Decision on WMS Investment.
In summary, the question of “How much does a WMS system cost?” encompasses various components, including licensing, implementation, hardware, training, and ongoing support costs.
However, the potential benefits—in terms of enhanced inventory management, improved order management, and increased efficiency—often justify the investment. By carefully considering the WMS pricing models available, understanding the total cost of ownership, and planning for future growth, businesses can select the right WMS that aligns with their operational goals and ensures a clear path to long-term ROI.
Ultimately, investing in a WMS is not just about managing costs; it’s about positioning your business for success in an increasingly competitive landscape. By embracing the right WMS solution, businesses can streamline their warehouse operations and achieve sustainable growth.
Disclaimer: Cost Estimates Based on Market Trends
The costs mentioned in this article are rough estimates based on current market trends. They can vary depending on specific business needs, customisation, and integration requirements. As every company’s requirements are unique, we recommend discussing your specific situation with a Balloon One consultant to get a more accurate quote tailored to your operations.
Frequently Asked Questions.
The average cost of a WMS varies significantly depending on the type of system and the company’s specific needs. Small businesses may find entry-level solutions for around £5,000 to £20,000, while mid-sized businesses can expect to spend between £20,000 and £100,000. For large enterprises needing comprehensive features, costs may range from £100,000 to over £500,000. Subscription-based cloud options may also start at around £1,000 per month, depending on user count and features.
Several factors influence WMS pricing, including the number of users, the company size, order volume, and the specific features required. Additionally, upfront costs for licensing, hardware, data migration, and training contribute to the total cost. Businesses should also consider ongoing support, maintenance, and potential upgrade fees, especially if they choose an on-premise solution.
Yes, hidden costs can arise, particularly around future upgrades, custom integrations, and operational changes that may require adjustments to the system. For example, adding new modules, integrating the WMS with other software, or scaling the system to support multiple warehouses can lead to additional expenses. Factoring these potential costs into the budget can help prevent unexpected expenses.